Schröding: Jakob Müller-Orgel, Tuntenhausen, Bj. 1869
Hier lesen Sie nun den ersten Teil der Geschichte der Restaurierung der Müller-Orgel von 1869 aus Schröding. Anders als alle anderen Berichte unter der Rubrik "bisherige Projekte", handelt es sich hier um die Zusammenfassung aller Wochenberichte aus 2020 und 2021, daher ist alles sehr detailiert und erfodert etwas mehr Zeit zum Lesen.
Starten wir mit dem Abbau der Orgel im Hebst 2020 ...
Die Orgel von 1869 hat 8 Register und ist rein mechanisch. Zuletzt war sie beinahe unspielbar, da einige Registerzüge klemmten.
Vermutlich wurde in den 1960ern das letzte mal Hand an diese Orgel gelegt, wie die dicke Staubschicht eindrücklich beweist.
Die Holzpfeifen sind original, von den Metallpfeifen sind dies nur noch Teile des Principal 8' und Octav 4'. Mixtur und Schwiegel stammen aus den 1960ern.
Ohne Pfeifen ist es nur noch ein hübscher Kasten. Die Rückwand trieb mir den Schweiß auf die Stirn, denn jederzeit hätte hier eine Füllung herabstürzen können.
Hier wurde in den 60er schon gearbeitet. Windlade und Stöcke wurden mit Liegelind-Ringen ausgestattet.
Schwerer als gedacht! Das "kleine" Lädchen hat einen massiven Eiche-Rahmen, welcher unsere ganze Kraft forderte.
Bevor die Orgel zu mir in die Werkstatt kommt, wird sie in einer anderen Kirche eingelagert, wo eine Begasung gegen Holzwurmbefall erfolgt.
Diese Tonne musste nun Stück für Stück (oder kg für kg) an der anderen Kirche wieder ausgeladen werden, diesmal ohne Unterstützung. Dank "Wagerl" waren aber auch die großen Trümmer wie Gehäusekranz und Windlade, kein Problem.
Nach ca. 2 Wochen konnte die Orgel aus der Begasung geholt werden und musste nun in meine "Großraumwerkstatt" einziehen. Anfangs war ich mir wirklich nicht sicher, ob alles einen Platz findet und ich anschließend noch arbeiten kann.
Kaum zu glauben, aber wahr - sämtliche Teile wurden im Anbau und auf dem Lagerboden verstaut, sodass ich keine Platzeinbußen hatte.
Nun konnten die ersten Arbeiten an der Orgel in Angriff genommen werden. Hier steht der Gehäusesockel, welcher erst einmal von den unpassenden Sockelleisten und allerlei Elektrik befreit werden musste.
Mit der Anzahl von Spax-Schrauben, mit welchen die 4 Sockelleisten angebracht waren, hätte man einen kompletten Carport errichten können. Natürlich war jede einzelne sauber verspachtelt und übermalt :-(.
Die Orgel soll künftig (wieder?) auf einem stabilen Bodenrahmen stehen. Dafür müssen zuerst die Positionen der Einbauten geklärt und vermessen werden.
Die Verteiler der Registermechanik waren mit wenigen Nägeln am Emporenboden fixiert. Der Rest der Orgel stand OHNE Fixierung auf der Empore. Lediglich Spieltisch und Trakturrahmen waren mit je zwei Schrauben befestigt.
----- 2021 -----
Im neuen Jahr startete die Überarbeitung der Holzpfeifen. Die eingesetzten und extrem verbeulten Blei-Labien, bereiteten mir anfänglich etwas Kummer.
Lösung brachte eine Technik, wie sie auch bei Metallpfeifen Anwendung findet - eine passende Innenschablone.
Durch diese konnten die Beulen nach außen gedrückt und dann mit dem Hämmerchen begradigt werden (gleiche Pfeife wie zuvor).
Die tiefen 9 Töne des Principal 8' sind aus Holz gefertigt, dann geht es mit Zink im Prospekt weiter.
Sie ließen sich nur mit roher Gewalt aus den Pfeifen holen, was weder den Pfeifen noch den Spunden samt Griffen gut bekommen ist.
Dann kümmerte ich mich um die zahreich abgebrochenen Schrauben der Vorschläge. Im Bild sieht man die erste Ausbeute incl. gebrochenem Bohrer.
Das Loch der herausoperierten Schraubenreste, wurden groß ausgebohrt und Querholzplättchen eingeleimt. So haben die neuen Schrauben wieder ordentlich Halt.
Ziel der Übung ist es, den Vorschlag wieder gut verschrauben zu können und nichts von der Reparatur zu sehen. Schräg eingedrehte Schrauben - IGITT!
Da -bis auf wenige Ausnahmen- die alten Spundgriffe ihren Dienst quittierten (Zapfen abgebrochen), mussten neue angefertigt werden. Hier liegen die Rohlinge dazu.
Am einzig verbliebenen, stabilen Spund, kann man das Übel gut erkennen. Das nur einfach kreuzverleimte Holz arbeitet sehr viel, das dünne Leder kann dies nicht ausgleichen = Pfeifenmündung platzt auf.
Die neuen Spunde sind aus mehrfach verleimter Schichtplatte und daher viel formstabiler. Außerdem werden die Spunde befilzt und beledert und können so das Arbeiten der Holzes (Pfeife) besser ausgleichen.
Damit die Griffe wirklich sicher in den Spunden sitzen, werden diese von unten verkeilt. Wieviel Kraft dabei ausgeübt wird, kann man gut daran erkennen, wie weit die beiden Buchekeile sich in den Fichtezapfen gedrückt haben.
Sieht nicht spektakulär aus, war aber viel Arbeit - der fertige Subbass mit neuen Spunden und Griffen, alle befilzt und neu beledert.
Zwischendurch läuft immer wieder die Reinigung der Eisenteile. Im Bild sieht man gut den vorher-nachher Zustand der Stockschrauben.
Nebenher wird auch "geforscht" und geplant. Mitten zwischen den Holzpfeifen sieht man drei Register Metallpfeifen (Bild vom Abbau), von denen nur noch der 4' (mittig) original ist.
Schon beim Abbau konnte man erkennen, dass auch die zugehörigen Stöcke nicht mehr original sind (anderer Farbton).
Der momentan disponierte 2' soll wieder durch eine Gamba 8', die 4-chörige Mixtur wieder durch eine 2- bis 3-chörige ersetzt werden. Im Bild werden gerade die Platzverhältnisse sondiert.
Die Stöcke vom jahrzehnte alten Schmutz zu befreien, ist eine wahre Kraftansrengung, aber es lohnt sich. Der rechte Stock ist vom Putzen noch leicht feucht, daher die intensive Farbe.
Auch in der Stirnansicht, sind die neuen von den alten Stöcken gut zu unterscheiden. Allerdings wurden für die neuen Stöcke die alten Unterfurniere verwendet.
Alle Stöcke und Raster sind nun sauber, die Maße für die Rekonstruktion der neuen Metallpfeifen ermittelt.
Auch hier gab es wieder einige Stimmvor-richtungen zu lösen, diesmal aber haupt-sächlich Stimmbleche der offenen Pfeifen.
Für die Rückführung der Disposition braucht es ja neue Stöcke, Raster und Rasterfüße. Letztere wurden nun schon einmal vorbereitet.
Nachdem die Maße vom Original abgenommen waren, wurde daraus eine Zeichnung erstellt und daraus wiederum das Maschinenprogramm generiert.
Auch das Bündel Holzpfeifen wurde nun durchgesehen und gerichtet. Hier ein paar Bilder aus dem "Schreckenskabinett".
Bei nahezu allen Holzpfeifen wurden schon mehrfach die Vorschläge entfernt und mal mehr mal weniger sorgsam wieder aufgleimt bzw. genagelt.
Offenbar gab es immer wieder Änderungswünsche an der Intonation, denn es wurden Aufschitte verändert und/oder Kernstiche entfernt.
Diesem "Umbau" lag kein Intonationswunsch zugrunde, hier wurde lediglich versucht, eine undichte Pfeife zum Sprechen zu bringen.
Hier ein Beispiel für eine wohltuende Außnahme. Diese Pfeife der Flöte 4' hat die letzten 152 Jahre in makellosem Zustand überstanden.
An den Spunden gab es auch wieder ein paar Reparaturen, dann wurde das Leder gepflegt und sie kamen wieder zurück in die Mündungen.
Da die Mensuren für die Rückführung der Disposition nun fest standen, traute ich mich auch an die ersten Vorbereitungen der Stöcke.
Da die Unterseiten (sog. Unterfurniere) noch alt sind (siehe Anschrieb), weden sie für die neuen Stöcke wieder verwendet.
Nach dem Entfernen der Dichtungen, wurden die Unterfurniere mit der Bandsäge vom Rest der Stöcke getrennt.
Nun startete die Demontage des Spieltisches. Da das Teil schon beim Abbau der Orgel einen "sensiblen" Eindruck machte, wurde es mit einem Spanngut gesichert.
Hier sieht man die Sicherung der Achsstifte an der Registermechanik. Das Aufleimen von Lederflecken auf den Stift, war gängige Praxis. Aber zusammen mit Weißleim (so meine Erfahrung), reagiert das Eisen viel aggressiver.
Die Holzverbindungen sind durchaus hochwertig. Hier sieht man auch gut, wie weit das Holz zurückgeschwunden ist, da die Zapfenverbindung allseits noch eine gute Passung hat. Die Eckverleimung ganz rechts, ist auch schon lose.
Nachdem ich die Lagerböcke der Registerschwerter ausgebaut hatte, flogen mir auch schon die ersten Gehäuseteile entgegen. Wenig später war der Spieltisch in seine Bestandteile zerlegt und konnte gut gereinigt werden.
Die stark verrosteten und teils quer gestellten Führungsstifte, waren schon mal kein gutes Vorzeichen.
Auch die Waagstifte sahen nicht viel besser aus. Der Waagbalken aus Eiche ist schon keine gute Wahl, wer aber auf die Idee kam, hier Lederscheiben unter zu legen, sollte heute noch bestraft werden.
Na ja, so richtig freuen konnte ich mich nicht. Zwar wurden die Tasten wieder schön sauber, aber der Schmutz der letzten Jahrzehnte musste teilweise mit dem Messer von den Tasten gekratzt werden.
Erst nach vollen zwei Arbeitstagen, war die Klaviatur wieder in einem ansehnlichen Zustand, zumindest von oben.
Von unten sahen die Tasten nämlich SO aus! Von den ursprünglich länglichen Führungsschlitzen, war nichts mehr übrig.
Da die "Gräben" oft läger waren, als die (Ober-) Taste breit, schied die herkömmliche Reparaturmethode aus (Loch bohren - rundes Plättchen einleimen).
Stattdessen wurde jede Taste einzeln in entsprechender Tiefe rechteckig ausgeklinkt, um maximalen Halt für den einzusetzenden Tastenboden zu gewährleisten.
Zwischendurch ging es mit dem gereinigten Klaviaturrahmen weiter, noch ohne Waag- und Führungsstifte.
Bevor die geputzten Stifte wieder an ihren Platz kommen konnten, mussten noch ein paar Schäden behoben werden.
War die Position korrekt, wurde mit etwas Druck ein Abdruck des Führungsstiftes auf der Tastenunterseite erzeugt.
Dann wurde die Taste in der Fräse fixiert und der Arbeitsbereich der Fräse mit dem Abdruck in Deckung gebracht.
Diese Arbeit war auch für mich Neuland und aufgrund der geringen Tastenabstände nicht einfach, aber nun liegt die Klaviatur wieder wie am ersten Tag in ihrem Rahmen (oder besser).
Nun kam das Spieltischgehäuse an die Reihe. Auf der Kreissäge liegt hier in Einzelteilen der "ehemalige" Frontrahmen.
Da die breiten Rahmenteile gebrochen und deutlich zu klein waren, wurden sämtliche Holzverbindungen gelöst, um die fehlenden Partien sauber ansetzen zu können.
Nach "ein wenig" Vorarbeit, wurde beim ersten Zusammenstecken das neue (alte) Maß der Bretter ermittelt.
Sieht nicht spektakulär aus, steckt aber viel Arbeit drin - die "neuen" Rahmenteile nach dem Verputzen, Anpassen und auf Maß bringen.
Zuvor muss aber sein "Bruder" noch überarbeitet werden. Hier wurde gerade ein breiter Riss verschlossen.
Bei der Test-Montage wurde höchstes Augenmerk auf die Passung gelegt, schließlich sollten die Einbauten wieder dort hin, wo sie vorher waren (alte Schraubenlöcher).
Hoffentlich war der Spieltisch jemals gerade, sonst bekomme ich ein Problem. Das angesetzte Stück am Rahmen (rechts von der roten Linie) misst oben 3mm, unten aber gute 11mm.
Nur zusammengesteckt, steht der Spieltisch nun schon ein vielfaches stabiler als vorher, aber die Verleimung muss noch warten.
Erst muss der Klaviaturträger noch saniert werden. Hier sieht man die starken Furnierschäden im Bassbereich (links neben der Klaviatur).
Das Trägerbrett ist zusammengeschwunden, dadurch wirft das quer zur Faser aufgeleimte Furnier deutliche Blasen.
Auch im Diskanbereich sieht es nicht besser aus. Hier wurde das Furnier schon einmal gerichtet, der Faserverlauf jedoch nicht berücksichtigt.
Da der Untergrund sehr schlecht war (Holzwurm, Ausbrüche, Pattex), waren umfangreiche Vorarbeiten notwendig (ausbessern, auffüllen mit Spachtel, abfräsen etc.).
Im Bassbereich wurden dünne Entlastungsschnitte gesetzt, das Furnier mit Leim unterspritzt und mit Zulagen und Zwingen wieder auf das Trägerbrett geleimt.
Im Bassbereich zeugen nur noch ganz feine Striche vom Eingriff. Die neue Schellackoberfläche befeuert das Nussbaumfurnier ungemein.
Nachdem die Schellackoberfläche fertig war, konnten die Einzelteile des Spieltisches verleimt werden.
Stabil, rechtwinklig und maßhaltig - diese Aussagen trafen hier schon lange nicht mehr zu, genau wie "der strahlend schöne Schellack".
Natürlich mussten immer wieder kleine Reparaturen durchgeführt werden, wie hier der Ersatz eines vom Wurm arg geschwächten Wellenärmchens.
Nun ging es mit dem Einbau der Klaviatur los. Um die Waagstifte nicht wieder den Gerbsalzen von Lederscheiben auszusetzen, kamen Unterlegscheiben aus Karton zum Einsatz.
Nicht nur das Nussbaumfurnier der Klaviaturblende erhielt eine Frischekur, auch "Herr Müller" wurde aufpoliert ;-).
Auch die fehlenden Deckelbretter wurden bereits angefertigt, mit Nutleisten an den Enden, wie es sich gehört.
Aber es gab noch noch ein paar Kleinigkeiten am Spieltisch zu machen, wie z.B. die hier gezeigte Frontfüllung.
Das ansich intakte Stück, ist im Laufe der Jahre um über 1cm zusammengeschrumpft, wie man an der Gratleiste gut erkennen kann.
Das führte dazu, dass ein Spalt zwischen Rahmen und Füllung sichtbar wurde und die Haltenase nicht mehr in den Rahmen reichte = Nase ohne Halt ;-).
Die Gratleisten wurden zurückgeklopft und ein passendes Stück Holz eingeleimt. Nach dem Verputzen mussten die Gratnuten nachgearbeitet werden, damit die Leisten wieder an ihren Platz konnten.
Die Einzelteile konnten zügig zusammengefügt werden, nur das Auflegen des Ladenkranzes war für einen allein etwas - na ja, "heikel".
Auch der Spieltisch passte wunderbar auf seinen Bodenrahmen, er ist ja jetzt unten genau so breit wie oben (war vorher nicht so).
Hier hat man den Blick durch den Spundzugang des Ladenkranzes auf die Ladenlager. Bei diesem Blick fiel mir auf, dass alles etwas schief in der Landschaft stand.
Nach ein paar Kontrollmessungen war klar, dass ein Großteil des Übels auf den Bodenkranz entfiel, welcher hinten gut 1 cm niedriger war, als vorne (bei 95cm Tiefe).
Weitere Setzungen/Ungenauigkeiten führten dazu, dass die Ladenlager an der Rückwand um gut 1,5 cm tiefer lagen, als vorne.
Am hinteren Querstück des Bodenkranzes, musste ein größeres Stück entfernt werden, da hier der Holzwurm ganze Arbeit geleistet hatte.
Allerdings kündigt sich schon das nächste Problem an, der Ladenkranz hängt vorne mittig ca. 1 cm durch, und das ohne Last.
Während ich über die Lösung des Kranzproblemes grübelte, widmete ich mich den Sockelblenden, welche um die Dicke des neuen Bodenrahmens verbreitert werden mussten.
Die kurzen Teile seitlich des Spieltisch-podiums, hatten die Demontage nicht gut verkraftet. Da auch hier z.B. schon die Gehrung abgeschnitten wurde, werden sie ersetzt.
Statik war nicht Müllers Paradedisziplin! Hier liegt das einzige senkrechte (mittige) Rahmenteil der Rückwand, welches die Last der Lade samt Pfeifen incl. Obergehäuse auf den Bodenkranz übertragen soll.
Allein mit dieser Aufgabe wäre das ca. 2 cm starke Brett schon überfordert. Zusätzlich gibt es aber noch eine Überplattung, welche das Rahmenteil auf die Hälfte schwächt.
Die Folge war das Einknicken des Rahmenteils, was zusammen mit dem schiefen Bodenkranz zur starken Rückwärts-Neigung der Orgel führte.
Nun konnte ich mich der Stabilisierung des Tragwerkes widmen. Hier sieht man eines der drei Ladenlager. Es wurde verm. für den Einbau des Windkanals geschwächt.
Sämtliche Ladenlager sind sauber in den Längsträger "geschwalbt". Leider ist der Lastpunkt aber zu weit vom Längsträger entfernt, sodass fünf der sechs Lagerpunkte gebrochen sind.
Da eine blose Verleimung der Lagerpunkte nicht halten und helfen würde, muss die Last besser abgefangen werden. Dafür wurden "Lagerschuhe" aus Buchensperrholz angefertigt, welche mit dem Längslager verschraubt werden.
Hier sieht man einen Lagerschuh am vorderen Längslager, welches bislang ohne mittlere Abstützung zum Boden auskommen musste.
Das "neue" Tragwerk. Die Ladenlager liegen sicher in Lagerschuhen, die Längslager wurden mit Abstützungen zum Bodenrahmen versehen. Die Ecken des Bodenkranzes wurden mit massiven Winkeln ausgesteift.
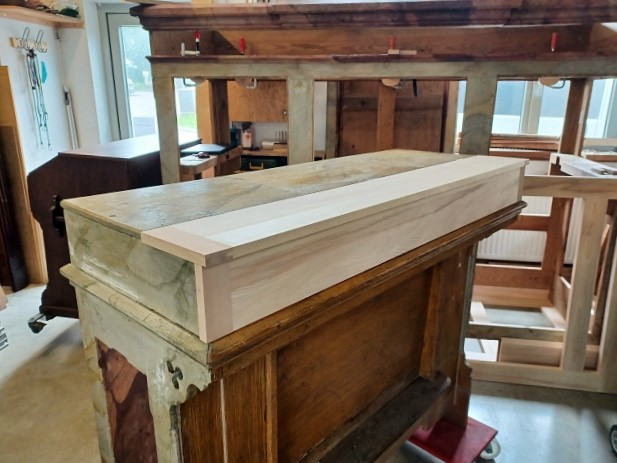
Auch am Spieltisch gab es noch etwas zu tun, die Scharniere für den rekonstruierten Deckel waren eingetroffen.
Dann konnten die Scharniere in ihre alten Aussparungen gesetzt und mit den Neuteilen verbunden werden.
An den letzten Holzpfeifen musste auch noch Hand angelegt werden. Die Reinigung war ja schon lange abgeschlossen, die Durchsicht stand aber noch aus.
Am Gedeckt hielten sich die Arbeiten in Grenzen. Ein paar Pfeifen mussten geleimt oder ausgegossen werden, anderen taten die Füße weh.
Ganz anders sah die Sache bei den offenen Flöten (8' und 4') aus. Die Deckelbretter aus Birnbaum, fand der Holzwurm schon früher lecker, was die vielen Reparaturspuren beweisen. Hier mussten sehr viele Pfeifen mit Warmleim ausgegossen werden.
Nachdem das Ständerwerk fertig war, ging es bei der "Müllerin" mit der Registermechanik los. Im Bild sieht man die massiven Schwerter, welche die Bewegung vom Boden auf Ladenhöhe übertragen.
Jedes, wirklich jedes Teil an dieser Orgel braucht Aufmerksamkeit. An den Schubstangen (oben) und Schwertern (unten) gab es diverse Ausrisse und -brüche zu beseitigen.
An den gereinigten Umlenkungen kann man gut erkennen, dass diese Winkel noch "feuergeschweißt" sind, also zusammen geschmiedet wurden.
Erst nach mehrfachem, kräftigem Abschrubben, zeigten die Holzteile wieder ihre originale Struktur und Farbe.
Ein paar Achslöcher mussten ausgebohrt, ausgestöpselt und neu gesetzt werden, da die Schrauben keinen Halt mehr hatten.
Dann ging es auch schon zur Montage. Nachdem die Fluchten ermittelt waren (vom Spieltisch und den Schwertern), wurden die Bretter auf dem neuen Bodnerahmen fixiert.
Schön langsam entsteht wieder ein Instrument. Im Zuge des Zusammenbaus, können auch immer mehr Fragen zur künftigen Windversorgung geklärt werden.
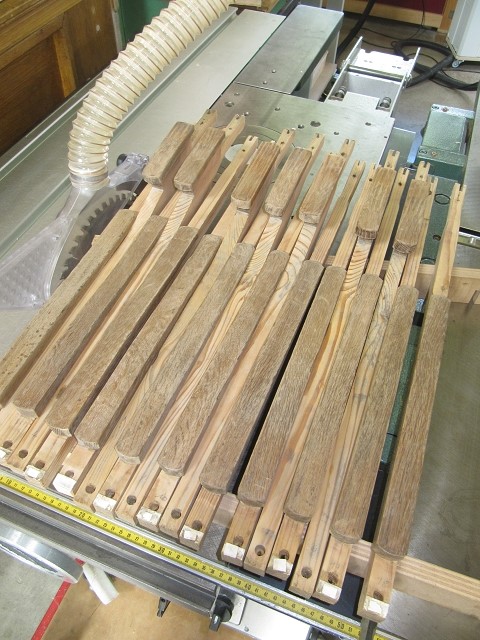
Zwischendurch wurde auch schon die Pedalklaviatur auf Vordermann gebracht. Vorsichtig wurden die Schandtaten früherer Malergenerationen von den Tasten entfernt.
Nachdem der Rahmen frisch verleimt und die Tasten geölt waren, sollte eigentlich der Zusammenbau erfolgen, aber erst mussten noch fast alle Tastenböden erneuert werden.
Nun standen auch Art, Weise und Dimension der neuen Windversorgung fest, daher konnte mit dem Zuschnitt des Materials begonnen werden.
Da der Werkstoff im wahrsten Sinne des Wortes "kostbar" ist, wurde alles erst einmal zu handsamen Platten verelimt.
Auch die Platte des unter dem Magazin hängenden Schöpfers, wurde aus Massivholz gemacht. Aus den aufliegenden rohen Kanteln, werden später die Gratleisten entstehen.
Hier steht einer der beiden Balgrahmen. Einer sitzt zwischen den Falten (Innenfalte / Außenfalte), der andere bildet oben den Abschluss.
Die neue Balganlage füllt bis auf wenige Zentimeter den komletten Unterbau aus (in Länge und Tiefe).
Da der Magazinbalg als sog. Doppelfaltenmagazin ausgeführt wird, gibt es zwei unterschiedliche Falten. Oben liegt die "normale", einwärts gewendete Falte, unten das Gegenstück, die sog. Außenfalte.
Um den Faltenscharnieren mehr Stabilität zu verleihen, wurden zunächst kreuzweise verleimte Bänder angebracht, ....
... bevor dann das innere Scharnierband aufgeleimt wurde. Links liegt die Innenfalte, rechts daneben die Außenfalte, ganz rechts die Schöpferfalte, jeweils von der kurzen Seite.
Wie auch beim Balg eines Druckwind-harmoniums, werden die Innenseiten der Faltenscharniere mit Leder überzogen. Nur ist hier alles etwas größer, dicker und schwerer.
Zwischendurch wurde auch die Balgplatte des Schöpfbalges weiter bearbeitet. Hier bin ich gerade mit dem Einfräsen die Gratnuten beschäftigt.
Die passend angefertigte Gratleiste verhindert ein Verziehen der Platte, gewährleistet aber, dass das Massivholz noch arbeiten kann.
Nachdem alles gut vorbereitet und verputzt war, konnten die Faltenpaare positioniert und angezeichnet werden.
Dann ging es auch schon mit den ersten Leinenbändern für die Innenfalten los, welche die Holzfalten auf dem Rahmen fixieren.
Auf die Leinenbänder folgten die Lederstreifen. Noch liegt alles auf dem Kopf. Die oben liegende, unbearbeitete Seite, wird später auf die Balgzarge geleimt.
Als Winddrossel sitzt über der Motoröffnung eine Klappe, welche über einen langen Hebel verschlossen wird, sollte der Balg seine "Voll"-Position erreichen. Die Klappe dient gleichzeitig als Rückschlagventil, sollte der Schöpfer zum Einsatz kommen.
Jetzt hat die Kopfsteherei ein Ende, hier ist alles richtig herum. Der Rahmen samt an ihn geleimter Innenfalten, wurde auf der Zarge ausgerichtet und mit den Leinenbändern fixiert.
Hier sieht man das massive Scharnier des Schöpfbalges, welches mit der Schöpferplatte und dem Zargenboden verschraubt ist (und schon wieder liegt alles auf dem Kopf).
Als nächstes werden erst viele Meter Lederstreifen verleimt, bevor es dann an die "spezielle" Außenfalte des Magazinbalges geht.
Da die Werkstatt noch nicht voll genug ist, waren Anfang letzter Woche die neuen Gamba- und Mixturpfeifen abzuholen.
An der neuen Balganlage ging es nach einem ersten Öffnungsversuch (Bild), an das Beledern der Faltenscharniere zur Zarge (unten).
Hier ein Blick ins Innenleben. Die großen Ausschnitte nehmen später die Schöpf- und Fangventile auf.
Nun ging es an die Vorbereitung der Außenfalte. Im Bild wurden gerade die Faltenpaare auf dem Rahmen ausgerichtet und mit der Hilfskonstruktion verschraubt.
Durch diese Hilfskonstruktion sind die Falten in ihrer Lage fixiert und trotzdem von beiden Seiten zugänglich.
Da später der Zugang nur noch schwer möglich ist, bekamen die Falten der Rahmenseite gleich ihren Überzug mit Blaupapier.
Als nächstes wurden die Falten wieder auf dem Rahmen fixiert, die Leinenbänder verleimt und die Hilfskonstruktion wieder entfernt.
Nachdem auch die zweite Seite papiert war, konnte das Paket aus Rahmen und Außenfalte auf dem Rahmen der Innenfalte fixiert und verleimt werden.
Bei einer Faltenbreite von gut 20 cm, haben die Zwickel jedoch schon eine etwas ausgedehntere Dimension.
Nach 5 Schaffellen und unzähligen Metern Lederband, war es nun geschafft, Ende der Leder- und Papierarbeiten.
Hier sieht man die Stirnseite des Schöpfers und den Ausschnitt für den Motoranschluss im Zargenboden.
Als wäre es so geplant gewesen. Die Länge des Schöpfers wurde durch ein originales Querlager bestimmt (oben links, über der Motorkiste).
Balg und Motorkiste sind nun fertig ..., na ja, fast - die oberen Platten zum Verschuss des Balges und die Scheren fehlen noch.
Nachdem es die Firma Laukhuff nicht mehr gibt und andere Zulieferer dadurch wochenlange Lieferzeiten haben, war das Motto bei den nun benötigten Balgscheren: selber machen.
Stahl ist zwar nicht mein Lieblings-werkstoff, aber so ein Ausflug ins Metallhandwerk, macht auch mal Spaß.
Die Balgscheren sorgen dafür, dass der Rahmen zwischen Innen- und Außenfalte gleichmäßig mit angehoben wird.
Üblicherweise würde man diese Scheren auf der Längsseite des Balges anbringen (4 Stück), aber die historischen Spuren waren hier eindeutig.
Die Maße des Hauptkanals (flach, aber breit), konnten anhand alter Spuren rekonstruiert werden. Der Anschlusskanal für den Motor (Bildmitte), weicht mit seinem Kropf einem Balglager aus.
Hier sieht man den eingebauten Anschlusskanal, welcher links mit dem Motor (in der Kiste) verbunden ist und nach oben in den Balg führt.
Deutlich zu erkennen sind hier die Ausschnitte im Träger der Registermechanik (re) und im Ladenlager (oben), welche die Maße für den Kanal vorgaben.
Nachdem die Kanäle an Ort und Stelle waren, folgte die Herstellung der mechanischen Schöpferbedienung.
Der sog. "Schwengel" liefert eine Bewegungsübersetzung von ca. 3:1, somit sollte der Pumpvorgang mit wenig Kraft zu bewerkstelligen sein.
So sieht es nun unter dem Schöpfer aus. Im offenen Zustand des Balges, liegt der Schwengel knapp unter der Schöpferplatte.
Die Schöpferplatte wird durch ein am Schwengel befindliches Rad nach oben gedrückt. Damit die Last etwas besser verteilt und das weiche Fichtenholz geschont wird, wurde die Platte mit einer Lauffläche aus Hartholz versehen.
Wer genau hinsieht, kann in diesem Bild die Arbeiten der letzten Wochen finden: Balg, Motorkiste, Kanäle, Schwengel.
Zum Abschluss wurde der Balg mit zwei verschraubten Platten verschlossen. Nun konnte der erste Test erfolgen.
Wunderbar! Der Balg ist dicht, die Scheren verrichten ihren Dienst, der Schöpfer samt Mechanik läuft seidenweich und schön leise.
Jetzt ging es mit der Überarbeitung der Windlade los. Wie man gut erkennen kann, ist das Teil noch mächtig schwarz, hier muss wohl "ein wenig" geputzt werden.
Doch zuvor kommt immer erst eine Bestandsaufnahme der Schäden. Hier sieht man z.B. alte, ganz alte und jüngere Belederungen - ein Zeichen für Problemstellen.
Auch die Kanzellenspunde wurden schon mehrfach geflickt und waren trotzdem wieder offen. So einen Riss mit einfachem Papier zu verschließen, ist eben nur eine kurzfristige Lösung.
Der Windkasten sah wenig einladend aus, obwohl die Ventile zuletzt ihrer Aufgabe halbwegs zuverlässig gerecht wurden.
Beim Ablösen des alten Leders wurde offenbar, was offensichtlich war - am Windkasten war keine einzige Verleimung dicht.
Sogar die Verleimung mit dem Ladenriegel war über die komplette Länge offen. So lies sich der Windkastenboden unter Einsatz sanfter Krafteinwirkung relativ leicht abheben.
Am Ruß kann man gut erkennen, dass es hier durch jede Ritze pfiff. Hier hatte ich fast den Verdacht, dass der Boden nie mit dem Rahmen verleimt war.
Die Risse, welche im hinteren Bereich mit Papier abgedeckt waren, zogen sich meist bis zum Ventilschlitz hin.
Das Zerlegen war abgeschlossen, nun musste gereinigt werden. Eine durchgängige Leimspur auf dem Ladenriegen und den Rahmenteilen verriet, dass der Windkastenboden eigentlich schon mit dem Rahmen hätte verleimt werden sollen - hat nicht geklappt!
Hier sieht man den gleichen Riss wie im vorherigen Bild, nur ohne Ladenriegel. Im hinteren Bereich sieht man alte Reparaturspuren. Da die Ventilfläche nach der Reparatur abgerichtet werden muss, musste leider das alte Papier entfernt werden.
Um die Risse auszuspanen, wurden dünne Leisten aus Eichen- und Fichtenholz hergerichtet. Die Risse wurden mit dünnen Fräsern soweit wie nötig, so schmal wie möglich ausgefräst, so haben die Leisten allseitig wieder eine saubere Leimfläche.
Ein paar Stunden später, war der Großteil der Arbeit erledigt. Alle Risse waren ausgefräst und mit Leisten verschlossen.
Schön - nicht wahr? Was hier wie von der Marketing-Abteilung hindekoriert aussieht, hat nichts mit Handwerkerromantik zu tun, sondern ist während dem Abrichten der Leistenüberstände entstanden.
Fertig! Beim vorsichtigen Abrichten der Ventilfläche fiel mir auf, dass zwei Rahmenteile deutlich tiefer lagen, diese wurden mit zwei Lagen Blaupapier aufgefüttert.
Auf der Schleifenseite sieht alles noch sehr gut aus. Die originale Belederung der Schleifenbahnen hielt die Kanzellen sicher beieinander und ist unversehrt.
Leider hatte man bei der letzten Überarbeitung auch Dichtungsringe auf die Lederbahnen geleimt (hätte verm. auf der Stockseite gereicht), aber das wird so belassen.
Allerdings mussten die vielen kleinen Dammerhöhungen weichen, da die meisten viel zu weit von den Stockschrauben entfernt aufgeleimt wurden (siehe vorh. Bild). Was noch zu sehen ist, sind Reste von altem Papier.
Die Lade an sich war nun soweit fertig, nun ging es an die Vorbereitung der Ventile. Als erstes wurde der Lederbelag entfernt.
Mut, Leichtsinn, oder nicht besser gewusst - das ist hier die Frage. Original waren die Ventile mit nur einer Lederschicht belegt, was sicher sehr laut und wenig betriebssicher war. Bei der letzten Überarbeitung leimte man daher eine zweite Lederschicht auf den alten Belag, was die Sache vermutlich nur wenig verbesserte. Im Bild sieht man das "neue" Leder, welches noch in gutem Zustand war.
Die nächste Baustelle waren die Ventilabzüge samt Windkastenboden. Zuerst stand wieder die Reinigung auf dem Programm, wobei das Papier auf der Innenseite erhalten blieb.
Hier sieht man die Außenseite des Bodens (hatte nie Papier). Die Abzugsdrähte mussten mit Stahlwolle abgerieben werden, um Schmutz und leichte Korrosion zu entfernen.
Zum Schutz des Blaupapiers, wurde auf der Innenseite mit Unterlage gearbeitet. Die winddichte Durchführung durch den Windkastenboden (sog. Pulpete), wird hier über einen einfachen Streifen durchbohrtes Messingblech bewerkstelligt.
Dann war es Zeit für das neue Papier. Damit nicht gleich wieder Risse entstehen, kam Leinenpapier zum Einsatz, welches enorm reißfest ist.
Zur Sicherheit wurde auch der hintere Bereich mit Papier beleimt. Um eine gute Verleimung von Lade und Ladenriegel zu gewährleisten, wurde diese Leimfläche nicht papiert.
Nach dem Aufschneiden der Ventilschlitze, sowie dem Aufleimen des Ladenriegels, konnten die gereinigten Ventilstifte wieder eingeschlagen werden.
Zur Kontrolle des Ventilsitzes, wurden alle Ventile nun in ihre Stifte gelegt. Bei den meisten war die Auflagefläche in Ordnung, ein paar Ventile mussten seitlich aufgedoppelt werden (Ventilschlitz durch Risse verbreitert).
Der neue Ventilbelag besteht aus rel. festem Filz und Leder. So werden die Aufschlaggeräusche verringert, die Betriebssicherheit erhöht und das Spielgefühl nicht komplett verändert.
Die Löcher für den hinteren Ventilstift, wurden nach alter-Väter-Sitte ausgebrannt, um Korrosion am Stift zu verhindern.
Sieht alles schon sehr gut aus! Demnächst können die Arbeiten an der Lade verm. abgeschlossen werden.
Dann kam der "große" Augenblick, der Winkastenboden wurde wieder (diesmal aber richtig) mit der Lade verleimt.
Da der Windkasten nun komplett war, konnten auch die Federn wieder eingesetzt und ausgerichtet werden. Die Federkraft wird erst bei der endgültigen Montage eingestellt.
So zieht die Mechanik die Ventile auf. Zwar haben die Ventilanhängungen ein "anti-klapper-Leder" verbaut, trotzdem sorgt hier Metall-auf-Metall für ordentlich Geräusche.
Zum Schluss bekamen die Spunde eine neue Dichtung aus Filz und Leder, dann waren die Arbeiten an der Lade vorerst erledigt.
Da vor dem Einbau der Windlade das Wellenbrett an seinen Platz muss, ging es nun hier an die Überarbeitung.
Der Ausbau der Wellen sorgte gelegentlich für ordentliches Stirnrunzeln. Bei manchen Wellen staß der Stift nur ca. 1,5mm im Lagerdöckchen.
Und natürlich war alles mit einer dicken Schicht aus Staub und Schmutz bedeckt (vorne vor - hinten nach der Reinigung).
Die Reinigung macht die Teile nicht nur sauber, man entdeckt dabei auch (viele) verdeckte Schäden, wie lose oder angebrochene Wellenärmchen.
Nach dem Beheben der Risse, wurden die aufgeschraubten Gratleisten (nur die mittlere ist tatsächlich eingegratet) neu verschraubt und so gesetzt, dass die langen Träger parallel und lotrecht montiert werden können.
Zwischendurch wurden die neuen Ersatzteile angefertigt. Lieber ein paar Stück mehr, so hat man auch später noch Ersatz.
Gemäß des Originals, wurden die neuen Döckchen aus Rüster (zum Glück hatte ich noch ein kleines Brett) angefertigt.
Da das Wellenbrett unter der Windlade hängt und die Arbeit über Kopf unangenehm ist, wurde die Montage vorab auf der liegenden Windlade durchgeführt.
Dabei wurde der (ein) Grund für die vielfach krummen und schiefen Einbaumaße dieser Orgel offensichtlich.
Der Grund war verm. mangelnde Präzision. Allein bei der Ausrichtung des Wellenbrettes zur Windlade, lag der damalige Orgelbauer rund 6mm daneben.
Zusammen mit den Wellen und den Trägern, hat das Wellenbrett ein ordentliches Gewicht, daher bemühte ich für die Montage meinen Aufzug.
Passt! Bis die Windlade an Ort und Stelle ist, bleibt das Wellenbrett nur leicht fixiert an seinem Platz.
Um mit dem Aufzug auf den Bodenrahmen und IN das Gehäuse fahren zu können, musste dies um 7mm angehoben werden.
Hier ist die Lade schon in Position, bereit zum Ablassen. Das aufgebockte Gehäuse ist gut zu erkennen (unten am Aufzug).
Hier ein Blick von hinten in den Inneraum. Man sieht unten den neuen Balg samt Kanal zur Windlade, sowie die Rückseite des Wellenbrettes.
Zwar ist alles geplant und sicher 100mal nachgemessen, aber trotzdem ist man froh, wenn am Ende alles passt. Zwischen Wellenbrett/Balg und Balg/Rückwand sind nur 15mm Platz.
Hier liegen die abgetrennten Unterfurniere der 4 neuen Stöcke, da die Disposition zurückgeführt wird.
Das Material für Stöcke und Raster wurde vorbereitet, die speziellen Rasterfüße schon im März angefertigt.
Die nächsten Tage standen ganz im Zeichen der neuen/alten Register. Im Bild sieht man die noch verpackten Pfeifen der Gamba 8' liegen.
Um die Maße für Stock- und Rasterbohrung abnehmen zu können, wurde die Verpackung teilweise oder ganz entfernt.
Ohne Papier war die Sache schon wesentlich übersichtlicher. Gemäß dem Original (Referenzorgeln), wird die Mixtur im Bassbereich 2fach und nur im Diskant 3fach.
Die ermittelten Daten wurden erfasst und werden als nächstes in die Zeichnung übertragen. Stöcke und Raster werden dann an der CNC-Fräse gefertigt.
Da bis auf 6 Pfeifen der Octav 4' zusammen mit der neuen Mixtur auf einem Stock steht, mußten auch diese Pfeifen vermessen werden.
Die letzten Tage verbrachte ich viel am PC, u.a. mussten die Daten der abgemessenen Pfeifen ins Zeichenprogramm übertragen werden.
Diese Zeichnung wächst seit Beginn der Arbeiten am Instrument und lieferte mir bislang wertvolle Erkenntnisse.
Soweit der Stand der Dinge am Jahresende 2021! Die Fortsetzung und Fertigstellung im Jahr 2022 finden Sie hier.