|
|
|
|
|
|
|
Oberschweinbach, Germany: |
|
|
|
Burger, Leipzig, Built in 1928 |
|
|
|
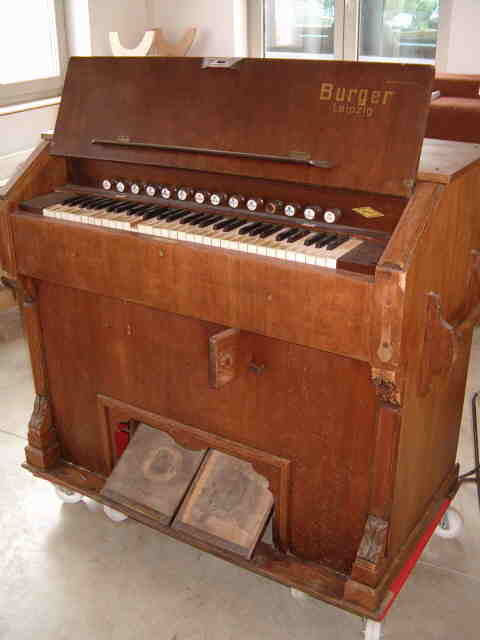 |
|
This reed organ was an eBay purchase. For €100, it was mine to collect from a garage near Landsberg. |
|
|
|
|
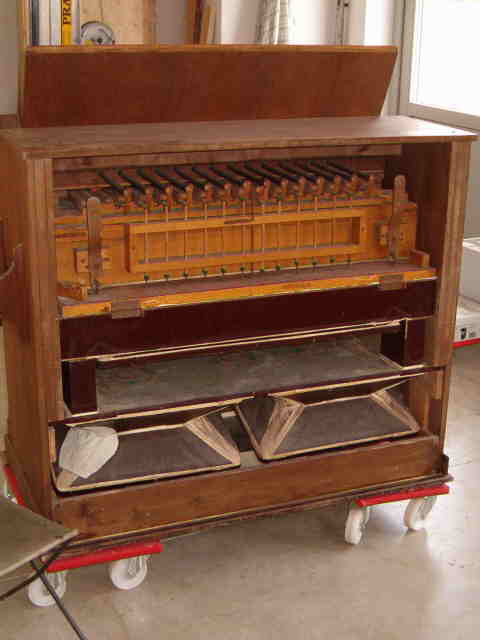 |
|
Absolutely unplayable and smelling strangely, was a pretty accurate description of the instrument's state. |
|
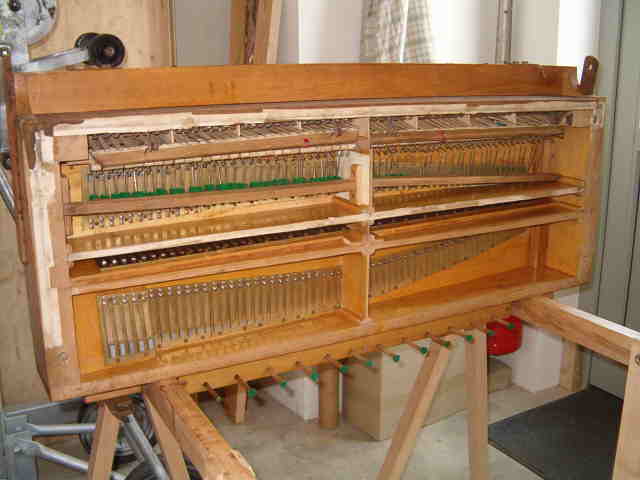 |
|
|
The three-part division after its removal. Material of all kinds had been glued to the frame in an attempt to make it leak-proof. The picture clearly shows the absolutely desolate state of the percussion. |
|
|
|
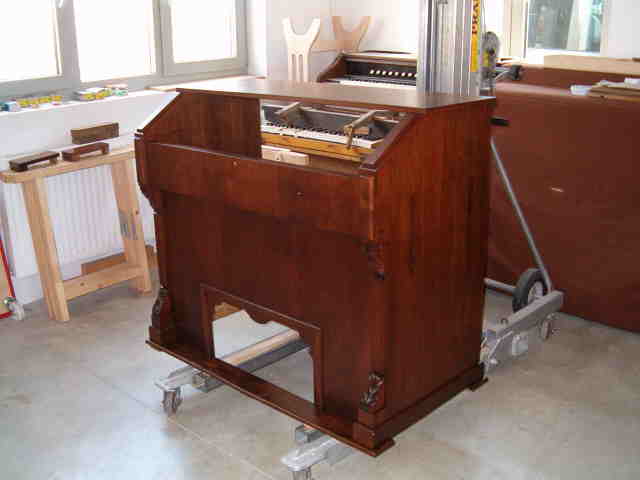 |
|
Before attending to the interior, we restored the case to a respectable appearance. After removing the old varnish, repairing all damage and re-staining the wood, several layers of clear varnish were applied. We purposely did not restore the shellac surface since the instrument was later intended to be rented out. |
|
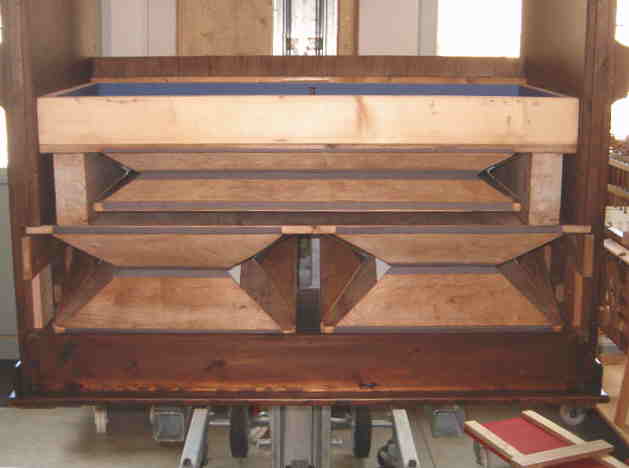 |
|
|
|
Next, we dealt with the bellows. The old glueing stuck particularly well, so removing it was a very time-consuming job. By the time this picture was taken, all had been forgotten and restoration work was in full swing. |
|
|
|
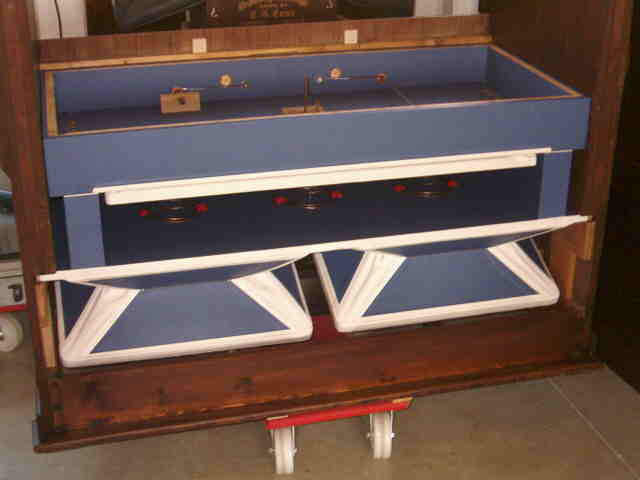 |
|
A few hours later, the bellows looked much better. Thorough preparatory work, premium-quality materials and precise workmanship are the key factors to crafting good reed organ bellows. |
|
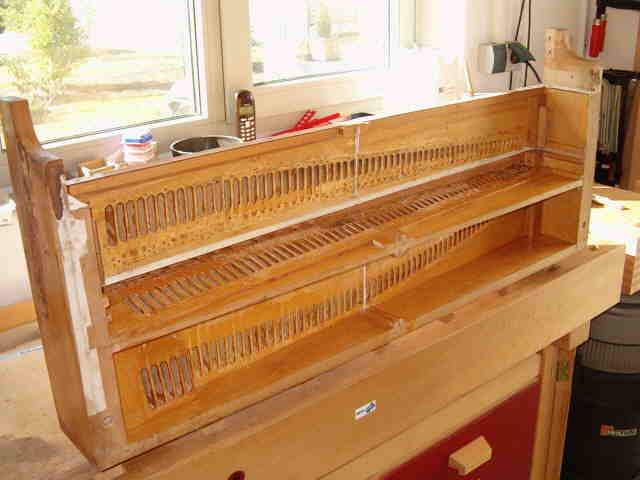 |
|
|
|
Next in line was the windchest. The picture shows it completely stripped and disassembled. The surfaces where the free reeds are mounted were sanded with a sanding block, and all other surfaces were lightly sanded down. Finally, shellac was applied. |
|
|
|
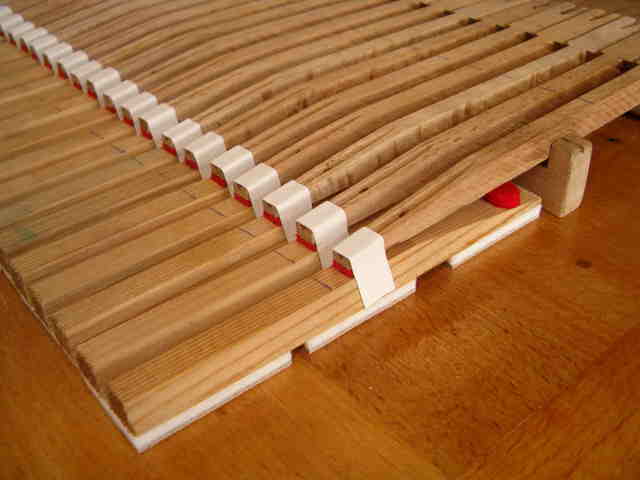 |
|
Here, the re-lined valves are back in place. All the felt and leather parts of this instrument were replaced. This included the felt cushions on the backfalls and the leather cuffs of the valves. |
|
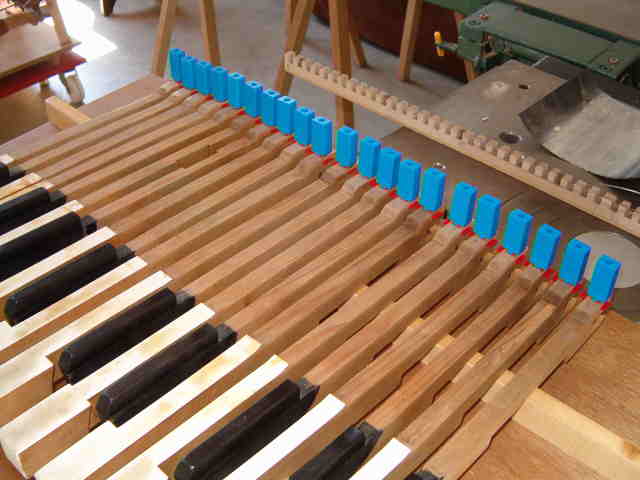 |
|
|
|
The keys received new felt guides to give them a "new" feeling when played. Next step was to send the keyboard to the console maker to be relined. |
|
|
|
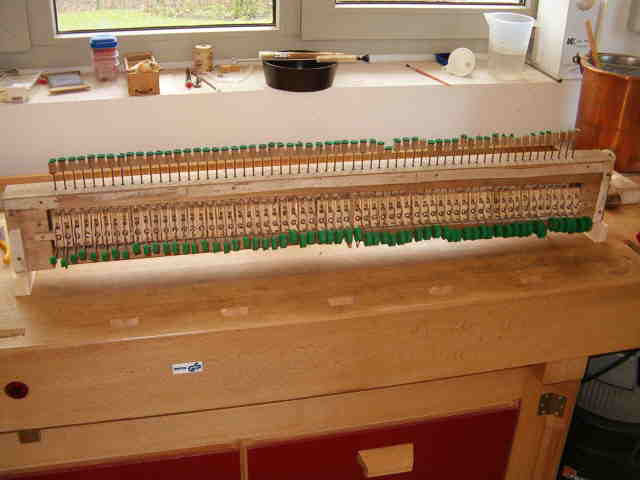 |
|
Probably the most difficult repair to the windchest was the work on the percussion. The picture shows it still mounted in its original state. What is does not show, however, is that hardly any of the little hammers would drop down freely. |
|
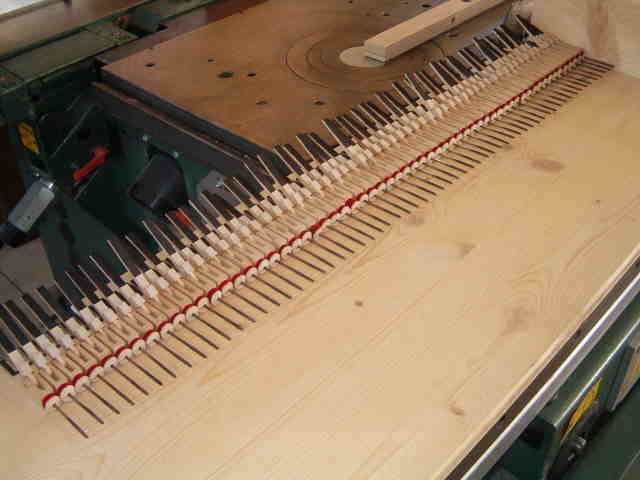 |
|
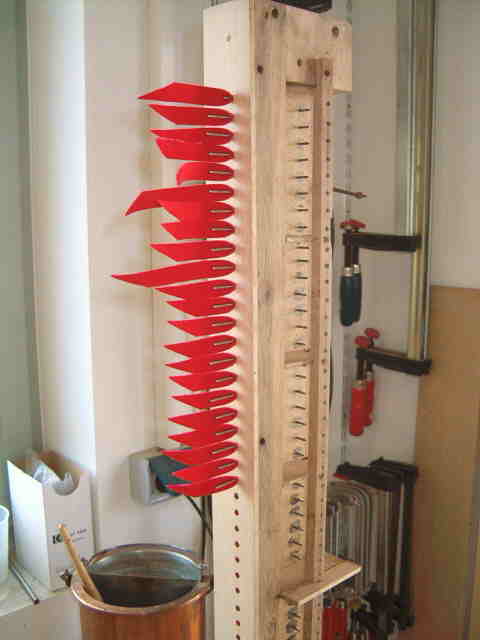 |
|
Fork-end blocks with free reeds, removed and overhauled. Work steps included making the mechanics move smoothly, replacing the leathers, adjusting the springs, replacing the damper felts and leather seals, and re-applying the graphite to the gliding surfaces. |
|
|
Above: The mechanical action controlling the valve backfalls was completely worn out and needed replacement. |
|
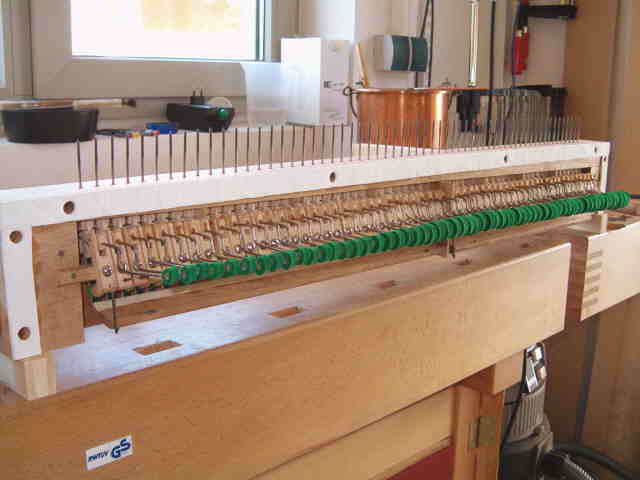 |
|
|
Here, work on the percussion is nearly finished. It is important that all parts move freely, that the action is precisely regulated and that all seals are leak-proof. |
|
|
|
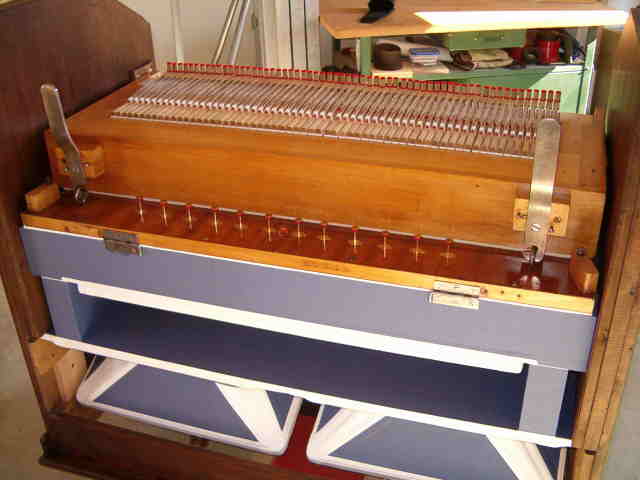 |
|
|
In the meantime, we had overhauled the stop table. New sealing bead was fitted and the windchest was sealed, eliminating the leakage problem. |
|
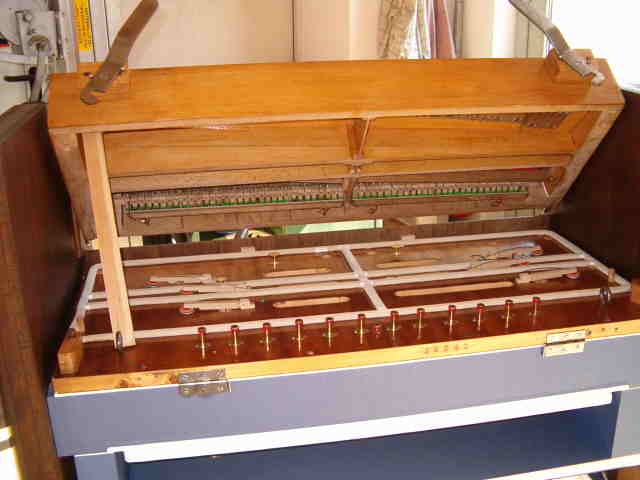 |
|
|
|
Another view, showing the new sealing bead. |
|
|
|
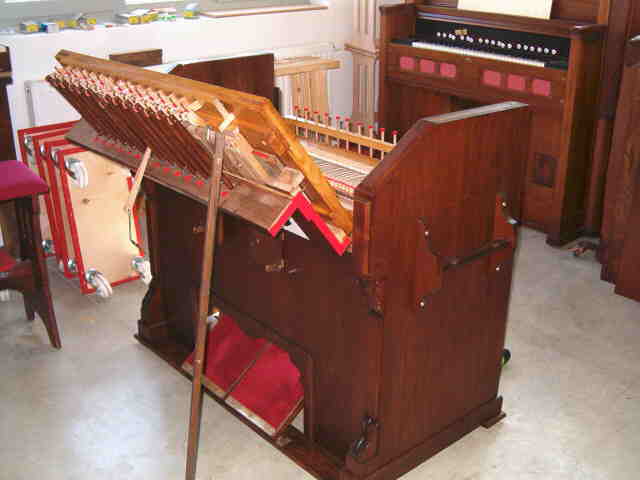 |
|
Once we had replaced the keyboard and stop mechanics, we adjusted the percussion and thoroughly tuned the instrument to 440 Hz. |
|
|
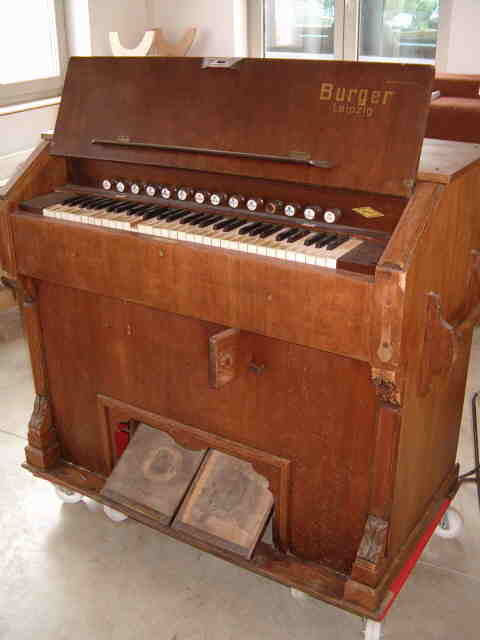 |
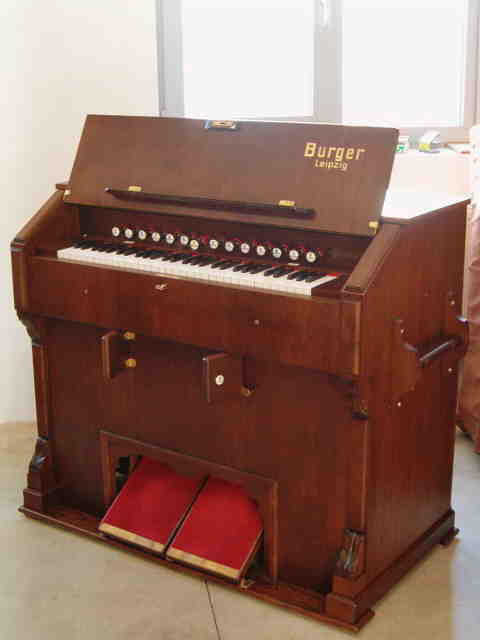 |
|
|
The instrument before and after the refurbishing. Approximately 270 working hours lie between these two photographs. |
|
Since completion of the restoration work, the instrument has been available for concerts only. One of the pieces in which it has performed particularly well to date is the Petite Messe Solenelle by G. Rossini. |
|
|
|
|
|
|
|
|
|
|
|
|
|
|
|
|
|
|
|
|
|
|
|
|
|
|
|